what is CNC machining?
CNC machining is a method of manufacturing that utilizes computer control technology to automatically process workpieces. By pre-programming a set of instructions, NC machines can perform precise machining operations with high accuracy, efficiency, and flexibility. NC machining is widely used in various industries such as mechanical engineering, aerospace, automotive manufacturing, and electronics.
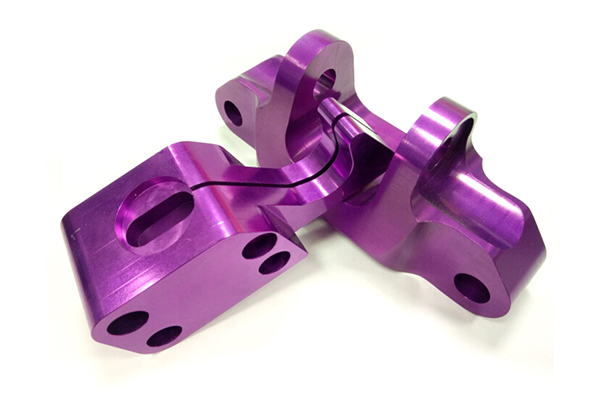
Basic Principles of CNC Machining
The basic principles of CNC machining involve controlling the machine tool’s movements and operations through a computerized control system. The following steps outline the key principles involved in CNC machining:
- Design and Programming:The first step is to design and program the machining operations. The program consists of a series of instructions, typically written in G-code or M-code, that guide the NC machine on how to perform the machining operations.
- Design and Programming:The first step is to design and program the machining operations. The program consists of a series of instructions, typically written in G-code or M-code, that guide the NC machine on how to perform the machining operations.
- Loading Programs and Setting Parameters:Before machining, the program is loaded into the NC machine’s control system. In addition, various parameters such as tool type, cutting speed, feed rate, and machining depth are set to meet the specific requirements of the workpiece.
- Machining the Workpiece:Once the program is loaded and parameters are set, the NC machine executes the machining operations. It controls the movement of different axes, as well as the rotation speed, feed rate, and cutting depth of the cutting tools, to accurately remove material and shape the workpiece.
- Monitoring and Inspecting the Machining Process:During machining, the NC machine continuously monitors and inspects the process. It collects and records data such as machining depth, cutting speed, and tool positions in real-time. These data can be used for quality control and process optimization.
- Completing the Machining and Outputting Results:After the machining process is completed, the NC machine provides the finished workpiece as the output. It can be directly removed from the machine or stored in an external device. Post-machining data analysis and optimization can be carried out if necessary.
In conclusion, numerical control machining is a sophisticated manufacturing process driven by computer control systems. It offers advantages such as high precision, efficiency, and quality. By following the aforementioned principles, NC machines can achieve accurate and effective machining, ultimately contributing to the improvement of industrial manufacturing.
Advantages and Features of CNC Machining Compared to Traditional Machining
The manufacturing industry has undergone significant advancements with the introduction of computer numerical control (CNC) machining. Traditional machining methods are gradually being replaced by CNC machining due to its numerous advantages and unique characteristics. In this article, we will explore the advantages and features of CNC machining in comparison to traditional machining methods.
- Precision and Accuracy:CNC machining offers exceptional precision and accuracy in producing intricate and complex components. Unlike traditional machining methods, which rely heavily on manual operation, CNC machines are controlled by computer programs that ensure consistent and repeatable results. The use of digital controls eliminates human errors, resulting in highly precise and accurate products.
- Enhanced Efficiency and Productivity:CNC machining allows for higher efficiency and productivity levels compared to traditional machining methods. With CNC machines, multiple processes such as milling, drilling, and turning can be performed in a single setup, eliminating the need for manual tool changes and reducing downtime. Furthermore, CNC machines operate at higher speeds and feeds, enabling faster production rates and shorter lead times.
- Flexibility and Versatility:One of the key advantages of CNC machining is its remarkable flexibility and versatility. CNC machines can easily adapt to different manufacturing requirements, making them suitable for a wide range of applications. By simply modifying the computer program, CNC machines can produce unique and intricate parts without the need for significant retooling or setup changes, resulting in cost and time savings.
- Consistency and Reproducibility:One of the key advantages of CNC machining is its remarkable flexibility and versatility. CNC machines can easily adapt to different manufacturing requirements, making them suitable for a wide range of applications. By simply modifying the computer program, CNC machines can produce unique and intricate parts without the need for significant retooling or setup changes, resulting in cost and time savings.
- Automation and Reduction of Human Error:CNC machining significantly reduces the dependency on manual labor and minimizes the risks associated with human error. By utilizing advanced computer programming, CNC machines operate autonomously, mitigating the potential for human mistakes and ensuring reliable and accurate production. This not only enhances the overall quality of the finished products but also reduces the need for extensive operator training.
- Improved Safety:CNC machining prioritizes operator safety through the integration of advanced safety features. These features include emergency stop buttons, protective enclosures, and automatic tool breakage detection. By minimizing the interaction between operators and machines, CNC machining provides a safer working environment, reducing the risks of accidents and injuries.
- Complex Design Capabilities:CNC machining offers the ability to manufacture complex and intricate designs that would be difficult or impossible to achieve with traditional machining methods. CNC machines can precisely execute complex toolpaths, allowing for the creation of intricate geometries, curves, and angles. This opens up new possibilities for innovative product design and engineering.
CNC machining has revolutionized the manufacturing industry by providing exceptional precision, efficiency, versatility, and automation. Compared to traditional machining methods, CNC machining offers superior accuracy, productivity, flexibility, and consistency. These advantages have positioned CNC machining as the preferred method for an increasing number of industries seeking to optimize production processes and deliver high-quality products. As technology continues to advance, CNC machining will continue to evolve, further enhancing its capabilities and advantages over.
Common Cutting Processes in CNC Machining
CNC machining is a widely used manufacturing process that involves the use of computer-controlled machines to create precise and complex parts. One of the key steps in CNC machining is the cutting process, where material is removed from a workpiece to create the desired shape and dimensions. There are several common cutting processes used in CNC machining, each with its own advantages and applications. In this article, we will explore some of these cutting processes.
1. Milling
Milling is one of the most versatile and widely used cutting processes in CNC machining. It involves the use of a rotating cutting tool to remove material from the workpiece. The cutting tool, also known as an end mill, has multiple cutting edges that remove material in a rotational motion. Milling can be done in various directions, including along the X, Y, and Z axes, allowing for the creation of complex shapes and features.
2. Turning
Turning is a cutting process that is primarily used for cylindrical parts. It involves rotating the workpiece while a cutting tool is fed into it to remove material and create a desired shape. Turning is commonly used for tasks such as creating round holes, threads, and cylindrical surfaces. It is a highly precise and efficient cutting process, making it ideal for high-volume production of cylindrical parts.
3. Drilling
Drilling is a cutting process used to create holes in a workpiece. It involves the use of a rotating cutting tool with two cutting edges, known as a drill bit. The drill bit is pressed against the workpiece and rotated to remove material and create a hole. Drilling can be done manually or using CNC machines. It is a fundamental cutting process in many industries, such as aerospace, automotive, and construction.
4. Grinding
Grinding is a cutting process used for precision machining of surfaces and materials. It involves the use of an abrasive wheel that rotates at high speed to remove material from the workpiece. Grinding is commonly used for tasks such as finishing, deburring, and shaping parts with tight tolerances. It is highly accurate and provides a smooth surface finish, making it suitable for applications where precision is crucial.
5. Laser Cutting
Laser cutting is a non-contact cutting process that uses a high-powered laser beam to cut through materials. It is commonly used for tasks such as cutting intricate shapes and patterns in various materials, including metals, plastics, and wood. Laser cutting offers high precision, high speed, and versatility, making it a popular choice in industries such as electronics, signage, and medical device manufacturing.
6. Waterjet Cutting
Waterjet cutting is a cold cutting process that uses a high-pressure jet of water mixed with abrasive particles to cut through materials. It is suitable for cutting a wide range of materials, including metal, stone, glass, and composites. Waterjet cutting offers flexibility, precision, and the ability to cut complex shapes without heat-affected zones or mechanical stress. It is commonly used in industries such as aerospace, automotive, and architecture.
In conclusion, CNC machining offers a wide range of cutting processes to create precise and complex parts. From milling and turning to drilling, grinding, laser cutting, and waterjet cutting, each cutting process has its own advantages and applications. By understanding the characteristics of these cutting processes, manufacturers can choose the most suitable method for their specific needs and achieve exceptional results in CNC machining.
How to ensure the accuracy of CNC machining
In the field of CNC machining, ensuring machining accuracy is of utmost importance. This article aims to discuss the various factors that affect machining accuracy and explore the methods and techniques employed to uphold it. By understanding these key factors, manufacturers can implement the necessary measures to achieve high precision in their CNC machining processes.
1. Introduction
CNC machining has revolutionized the manufacturing industry with its ability to produce complex and precise components. However, achieving the desired level of accuracy in CNC machining is not always straightforward. Several factors can influence the machining accuracy, and manufacturers must address these factors effectively.
2. Factors Affecting Machining Accuracy
2.1 Machine Tools
The quality and condition of the machine tools used in CNC manufacturing play a significant role in determining machining accuracy. Factors such as machine rigidity, stability, and precision must be carefully evaluated and maintained. Regular maintenance, calibration, and alignment of machine tools are essential to ensure their optimal performance.
2.2 Cutting Tools
The selection and condition of cutting tools directly affect machining accuracy. Dull or worn-out cutting tools can lead to poor surface finish and dimensional inaccuracy. It is vital to use high-quality cutting tools and regularly monitor their condition to maintain accuracy. Proper tool selection, including the choice of tool material, geometry, and coatings, can also greatly impact machining accuracy.
2.3 Workpiece Material
Different materials exhibit varying levels of machinability, which can affect machining accuracy. Factors such as hardness, heat resistance, and tendency to chip or deform influence the machining process. Manufacturers must understand the properties of the workpiece material and adjust cutting parameters accordingly to achieve desired accuracy.
2.4 Cutting Parameters
The selection and optimization of cutting parameters, including cutting speed, feed rate, and depth of cut, are critical for maintaining machining accuracy. Improper cutting parameters can lead to excessive tool wear, poor surface finish, and dimensional errors. Manufacturers must analyze and adjust cutting parameters based on the specific requirements of the workpiece to achieve the desired accuracy.
2.5 Fixturing and Clamping
The stability and accuracy of the workpiece during machining depend on the effectiveness of fixturing and clamping. Inaccurate or inadequate fixturing can result in workpiece movement or vibration, leading to machining errors. Proper fixturing design and secure clamping techniques are necessary to ensure workpiece stability and accuracy during machining.
2.6 Environmental Factors
Environmental conditions, such as temperature, humidity, and vibration, can affect machining accuracy. Temperature fluctuations can cause thermal expansion or contraction of machine components and workpieces, leading to dimensional variations. Controlling and maintaining stable environmental conditions within specified limits is crucial for achieving consistent accuracy in CNC manufacturing.
3. Ensuring Machining Accuracy
To ensure machining accuracy in CNC manufacturing, manufacturers can employ several methods and techniques:
3.1 Machine Calibration and Maintenance
Regular calibration and maintenance of machine tools are essential to maintain accuracy. This involves checking and adjusting the machine’s geometry, alignment, and lubrication systems. Routine inspections and preventive maintenance procedures should be implemented to identify and address any potential issues promptly.
3.2 Cutting Tool Managemen
Effective management of cutting tools includes proper tool selection, regular inspection, and reconditioning or replacement when necessary. Implementing a tool life management system and monitoring tool wear can help maintain accuracy and minimize downtime.
3.3 Program Optimization
Optimizing CNC machining programs involves utilizing advanced software tools to analyze toolpaths, minimize cutting forces, and optimize cutting parameters. This can help maximize efficiency, improve surface finish, and reduce dimensional errors.
3.4 Quality Assurance Measures
Implementing stringent quality assurance measures, such as inspecting finished components using coordinate measuring machines (CMMs) or other measurement tools, can help verify the accuracy of the machining process. Dimensional tolerances and surface finish requrements should be carefully monitored and verified against specifications to ensure compliance.
3.5 Process Monitoring and Feedback
Monitoring the machining process in real-time can provide valuable feedback to detect and correct any deviations from the desired accuracy. Utilizing sensors, such as vibration sensors or force sensors, can help identify issues such as tool wear, excessive vibrations, or material inconsistencies. This allows for proactive adjustments and improvements to maintain accuracy throughout the machining process.
3.6 Employee Training and Skill Development
Continuous learning and skill development initiatives ensure that operators have the necessary knowledge and expertise to perform tasks accurately. Regular training sessions and workshops can be conducted to update employees on the latest machining techniques, equipment advancements, and quality control methodologies. By investing in employee training and skill development, manufacturers can cultivate a skilled workforce that is capable of upholding machining accuracy to the highest standards.
4. Conclusion
Achieving and maintaining machining accuracy is a crucial aspect of CNC manufacturing. Various factors, including machine tools, cutting tools, workpiece materials, cutting parameters, fixturing, and environmental conditions, can influence machining accuracy. By addressing these factors and implementing appropriate measures, such as machine calibration and maintenance, cutting tool management, program optimization, and quality assurance, manufacturers can ensure precision and accuracy in their CNC machining processes. Moreover, providing comprehensive employee training and skill development opportunities fosters a competent and knowledgeable workforce that can consistently uphold machining accuracy. By prioritizing accuracy, manufacturers can achieve high-quality products, customer satisfaction, and long-term success in the CNC manufacturing industry.