Custom Sheet Metal Fabrication Services
sheet metal fabrication refers to the process of processing sheet metals into various shapes and dimensions according to specific requirements, including cutting, bending, stamping, assembling, surface finishing, etc.
Sheet metal fabrication is one of the important manufacturing processes in various industries such as automobiles, railways, ships, aviation, electronics, and household appliances.Sheet metals are widely used in these industries due to their characteristics such as high strength, light weight, good heat
resistance, good corrosion resistance, and good malleability.
Sheet metal fabrication requires high-precision equipment and skilled technicians to ensure high-quality products.sheet metal fabrication typically involves a series of processes such as sheet metal blanking, sheet metal bending,sheet metal stamping, sheet metal welding, sheet metal surface finishing,sheet metal assembly, etc.

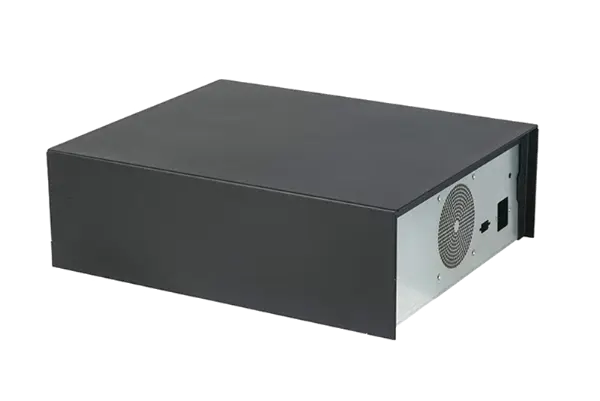
What Is the Sheet Metal Fabrication?
Sheet metal fabrication is a process of shaping and manipulating sheet metal through cutting, bending, and assembling techniques to create various metal structures and products. It involves the use of specialized tools and machinery to cut precise shapes and sizes, forming complex structures for a wide range of industries such as automotive, aerospace, construction, and manufacturing. Sheet metal fabrication is crucial in producing components like enclosures, brackets, panels, and frames with high precision and durability. Overall, sheet metal fabrication plays a vital role in modern engineering and manufacturing processes.
How Does Sheet Metal Fabrication Work?
Sheet metal fabrication process involves several key steps.
Firstly, the sheet metal material is selected based on the desired properties like thickness and durability. Then, the material is cut using shearing, laser cutting, or water jet cutting methods to achieve the required shape.
Next, the metal is formed through bending, rolling, or stamping to create the desired structure. Following that, welding, fastening, or adhesive bonding techniques are used to join multiple pieces together.
Finally, finishing processes such as painting, coating, or polishing are applied to enhance the appearance and protect the surface. Overall, sheet metal fabrication is a precise and intricate process that requires skilled craftsmanship and specialized equipment.
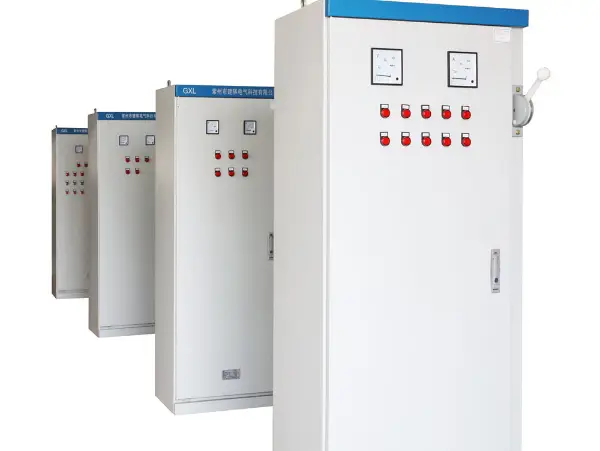
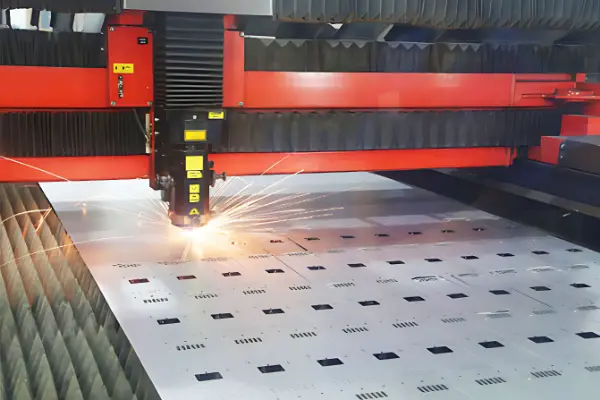
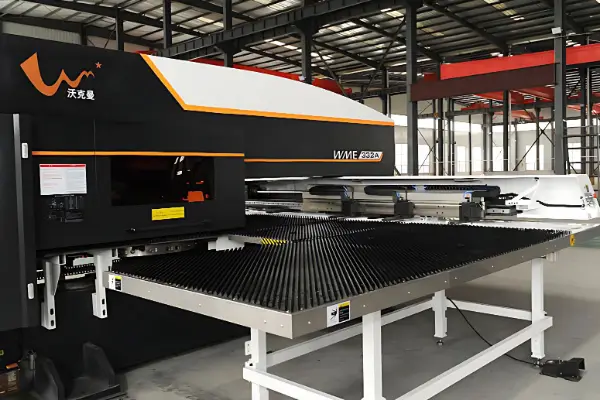
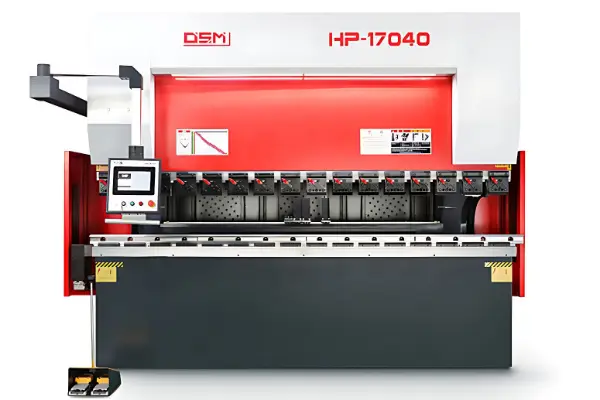
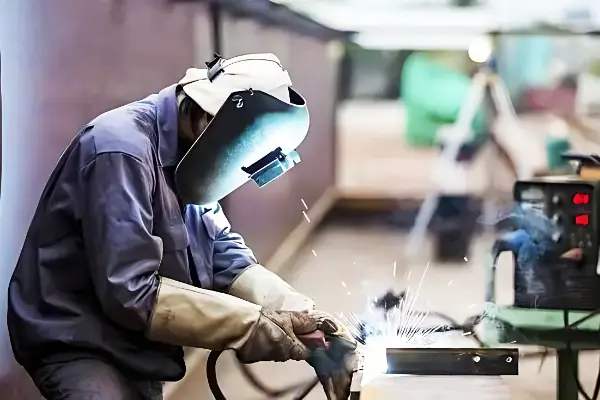
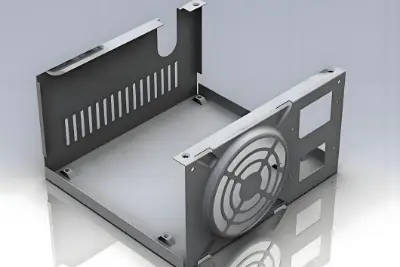
If you would like to specify a customized material for your application, please contact us or request an online quote now.
Feature | Tolerance |
---|---|
Size | 47 in. x 119 in. OR 1,193.8mm x 3,022.6mm (max) |
Formed part | 1.5 in. x 1.5 in. OR 38.1mm x 38.1mm (min) |
Flat part | 0.5 in. x 0.5 in. OR 12.7mm x 12.7mm(min) |
Bend length | 10 ft. OR 3.048m (max) |
Feature | Tolerance |
---|---|
Bends | +/- 2 degree |
Offsets | +/- 0.024 in. (+/- 0.608mm) |
Bend to Edge | +/- 0.020 in. (+/- 0.508mm) |
Bend to Hole/Hardware/Bend | +/- 0.030 in. (+/- 0.762mm) |
Hole Diameters | +/- 0.010 in. (+/- 0.254mm) |
Edge to Edge/Hole; Hole to Hole | +/- 0.010 in. (+/- 0.254mm) |
Features Separated By Two or More Bends | +/- 0.060 in. (+/- 1.524mm) |
Hardware to Edge/Hole | +/- 0.020 in. (+/- 0.508mm) |
Hardware to Hardware | +/- 0.030 in. (+/- 0.762mm) |
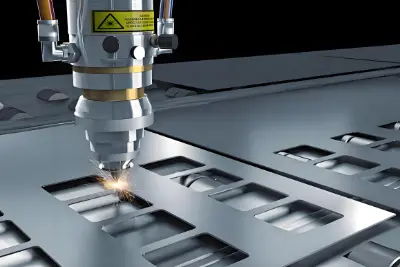
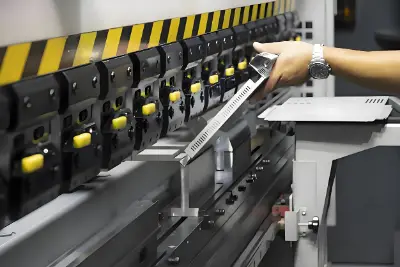
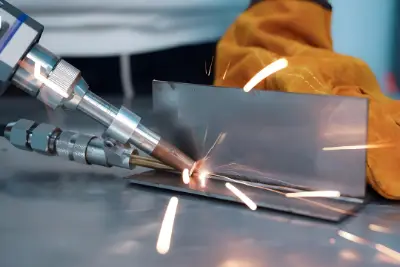