5-axis CNC machining service
With 5-axis CNC machining, we deliver precision, efficiency, and versatility. Our high-quality services enable the production of complex shapes with accuracy and speed.
5-Axis CNC Machining Offer Unrivaled Flexibility and Speed for Complex and Time-Sensitive Machining Parts.The 5-axis CNC machining provide unparalleled flexibility and speed for complex and time-sensitive machining parts. The experienced team at Centerk can help bring your ideas to life, from rapid prototyping to final parts for safety-critical applications. Our 4-axis and 5-axis milling capabilities enable us to deliver precision parts with complex geometries. For information on our conventional CNC machining services (including 3-axis CNC milling, CNC turning, and EDM), please visit our CNC Machining Services page.
What is 5-axis Machining
5-axis machining is a highly advanced manufacturing process that involves using a CNC machine with five axes of motion to create complex and intricate parts and components. Unlike traditional 3-axis machining, which operates on three orthogonal axes (X, Y, and Z), 5-axis machining adds two additional rotary axes, typically A and B, allowing for more flexible and dynamic tool movement.
The ability to move the cutting tool along five different axes enables 5-axis machining to produce parts with intricate details, smooth contours, and complex shapes that would be challenging or impossible to achieve with conventional machining methods. This technology allows for a higher level of precision and accuracy, as well as increased efficiency by reducing the need for multiple setups and tool changes.
5-axis machining is widely used in industries such as aerospace, automotive, medical, and tooling, where precision, quality, and intricate design are critical. It offers unmatched flexibility and speed in manufacturing critical components and is essential for producing high-quality parts with complex geometries.
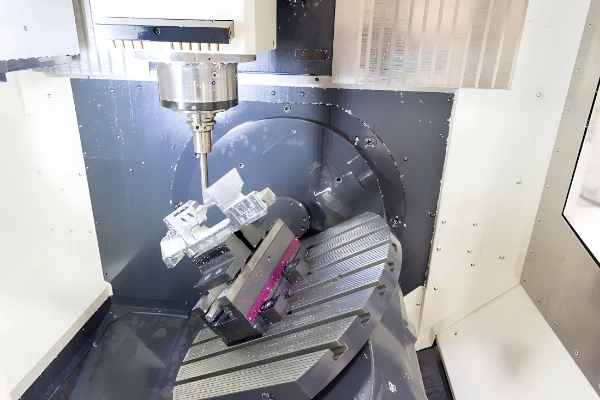
Advantages of 5 Axis Machining at Centerk
Quick Turnaround
5-axis CNC machining technology has the advantage of high-speed cutting and efficient processing, which can greatly shorten the processing cycle and improve production efficiency.
Machines with multiple axes can achieve one-time processing of complex parts, avoiding time wasted on multiple clamping and adjustments, thus achieving quick turnaround.
Quality Assurance
5-axis CNC machining equipment has high precision and good stability during the machining process, ensuring the precision and quality of parts.
Through CNC programming and precise control, 5-axis CNC machine tools can achieve high-precision machining of complex parts, ensuring that the product quality meets the requirements.
Industry Compatibility
5-axis CNC machine tools are suitable for multiple industries, such as aerospace, automotive, medical equipment, etc., for parts processing.
Different industries have different requirements for part precision and complexity. 5-axis CNC machining has flexibility and applicability to meet the processing needs of different industries.
Professionalism and Experience
5-axis CNC machining requires operators to have a certain level of professional knowledge and experience to write appropriate programs based on the characteristics and processing requirements of the parts.
Experienced operators can choose the appropriate processing technology based on part structure and material, ensuring processing efficiency and product quality
Emphasis on Employee Training and Technical Improvement
Companies should focus on training and skill improvement for operators, enabling them to proficiently operate and program 5-axis CNC machine tools.
Continuous improvement in employees’ technical skills and professional competencies can enhance processing efficiency and product quality, ensuring the company’s competitiveness and sustainable development.
Advanced Equipment
5-axis CNC machine tools adopt advanced control systems and automation technology, capable of achieving high-precision machining and complex surface machining.
The Haas 5-axis CNC machine tools we have purchased effectively ensure the precision of CNC machined parts.
Work with Us in 4 Simple Steps Only
With many years of manufacturing experience, Centerk offers the best solutions for all rapid prototyping and low-volume manufacturing needs. We streamline the innovation cycle into four simple but effective steps.
1.Upload Your Design
Simply upload CAD files and submitan RFQ online with clear information.
2.Design Analysis
We will provide you with professionalanalysis quotation.
3.Start Production
Our technicians will produce yourparts according to the drawings.
Receive Your Parts.
Our technicians will produce yourparts according to the drawings.
5-axis CNC Machining Applications
Through its diverse applications in the aerospace, automotive, energy, medical equipment, robotics, and semiconductor industries, Precision CNC machining has become a cornerstone of advanced manufacturing processes, enabling the production of intricate, high-precision parts that drive innovation and excellence across various sectors.
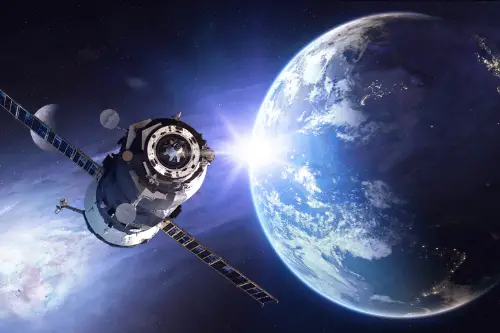
aerospace
The aerospace industry heavily relies on 5-axis CNC machining for the production of critical components used in aircraft, spacecraft, and satellites. From structural parts to engine components, 5-axis machines excel in manufacturing complex and high-precision parts required for aerospace applications. The ability to machine intricate shapes and contours with tight tolerances ensures the quality and reliability needed for the demanding aerospace environment.
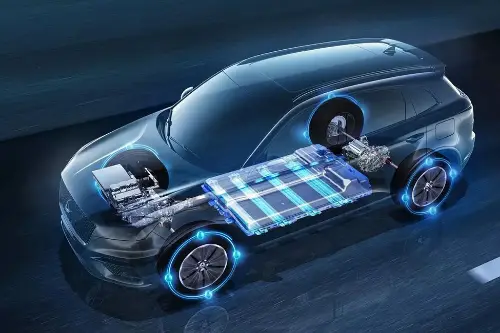
automotive
In the automotive sector, 5-axis CNC machining is instrumental in creating high-performance components for vehicles. Engine parts, transmission components, and chassis elements are manufactured with precision and efficiency using 5-axis machines. The capability to produce lightweight and durable parts with complex geometries enhances the performance and fuel efficiency of vehicles, meeting the stringent standards of the automotive industry.
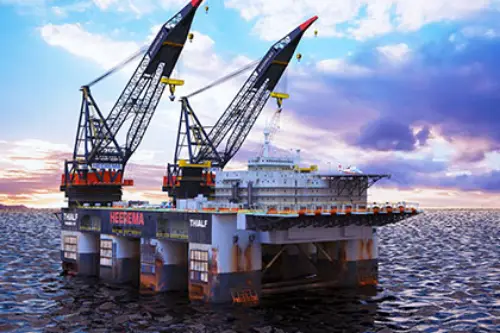
Energy
5-axis CNC machining plays a vital role in the energy industry, supporting the manufacturing of components for renewable energy systems, power generation equipment, and oil and gas machinery. From wind turbine components to drilling equipment, 5-axis machines offer versatility in producing intricate parts with superior accuracy and efficiency. This technology ensures the precision and reliability required for the essential components in the energy sector.
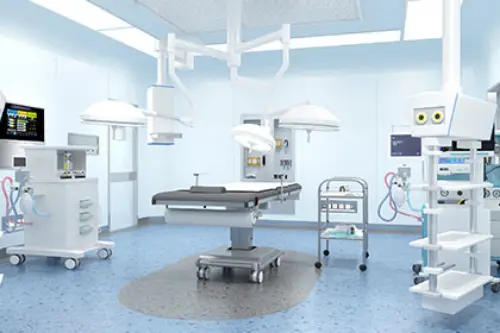
Amedical device
The medical equipment industry benefits significantly from 5-axis CNC machining for fabricating precise and customized components for medical devices, surgical instruments, and prosthetics. The advanced capabilities of 5-axis machines enable the production of intricate parts with complex geometries essential in the medical field. This technology ensures the accuracy, consistency, and quality necessary for critical healthcare applications, contributing to advancements in medical technology.
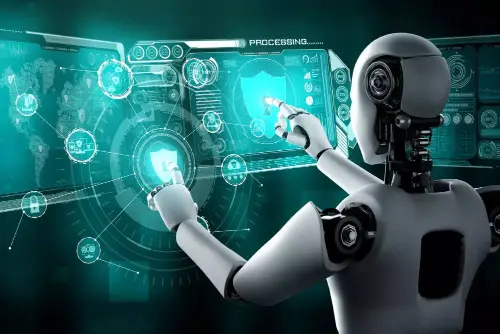
Robotics
In the robotics sector, 5-axis CNC machining is widely utilized for manufacturing components for robotic systems, automation equipment, and precision instruments. The ability to machine complex and high-precision parts allows for the development of advanced robotic solutions with enhanced functionality and performance. With the capabilities of 5-axis machines, robotics systems can achieve high precision, reliability, and efficiency in various applications, ranging from manufacturing to healthcare and beyond.
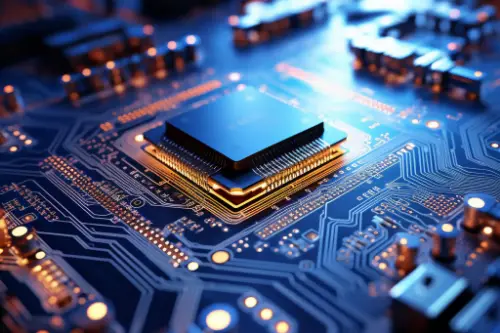
Your Attractive Heading
The semiconductor industry leverages 5-axis CNC machining for producing components used in semiconductor manufacturing equipment, microelectronics, and electronic devices. With the high precision and accuracy of 5-axis machines, intricate components with tight tolerances essential for semiconductor fabrication are manufactured efficiently. This technology ensures the production of high-quality components critical for the semiconductor industry’s technological advancements, supporting the development of cutting-edge electronic devices and systems.
5-Axis CNC machining Parts Display
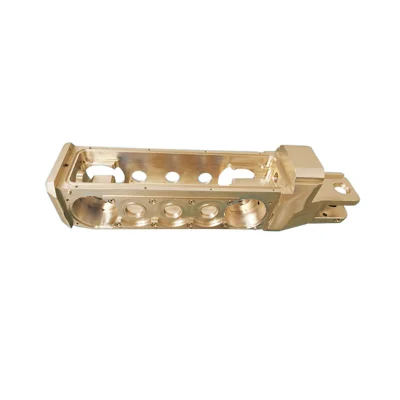
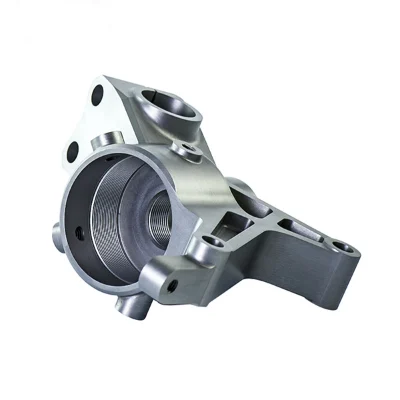
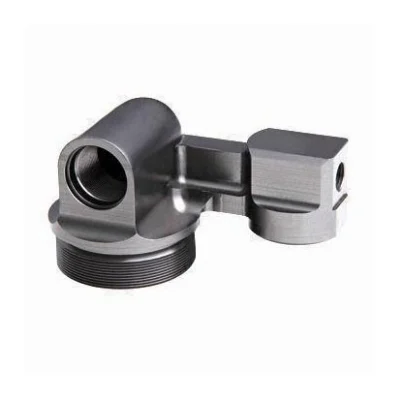
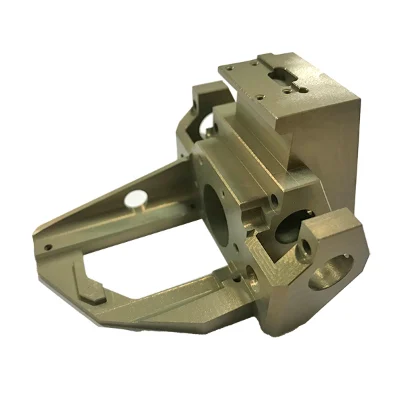
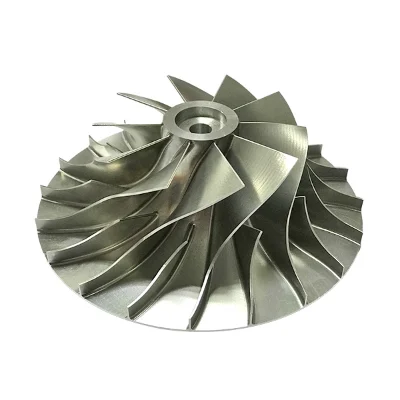
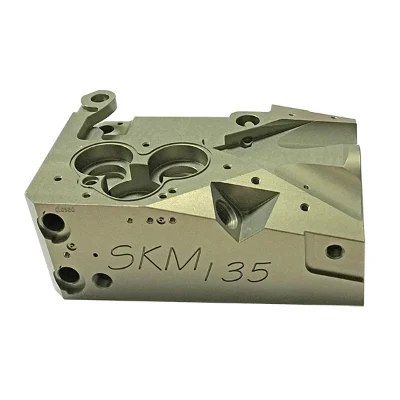
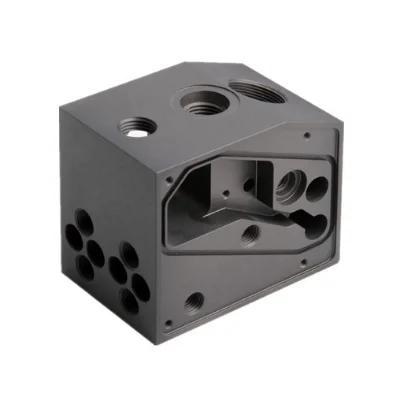
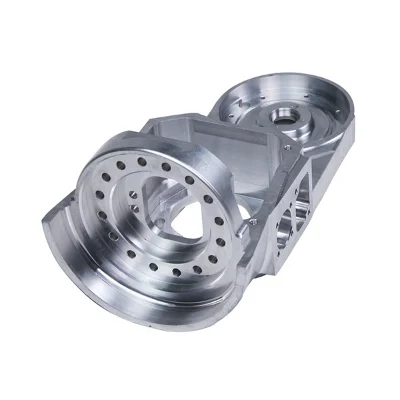
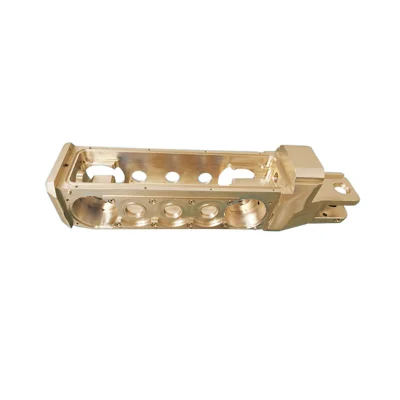
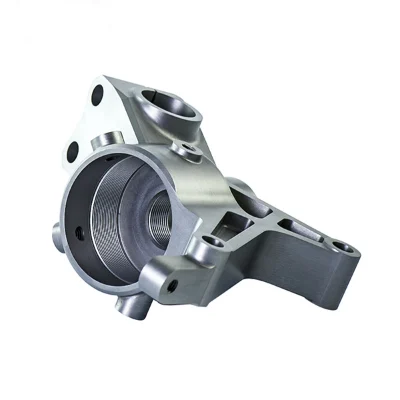
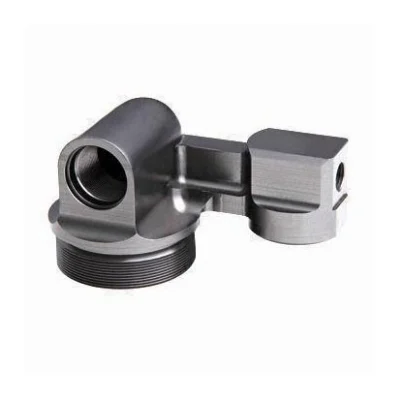
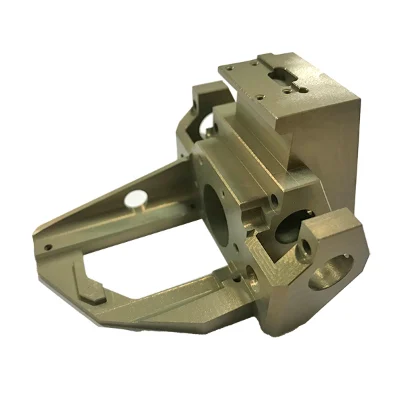
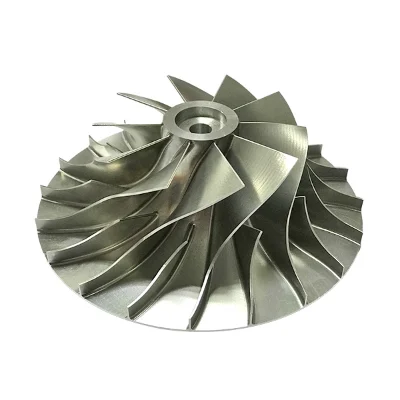
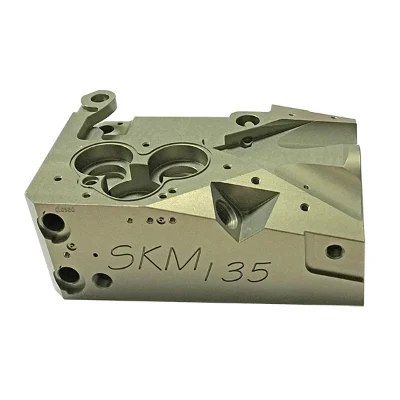
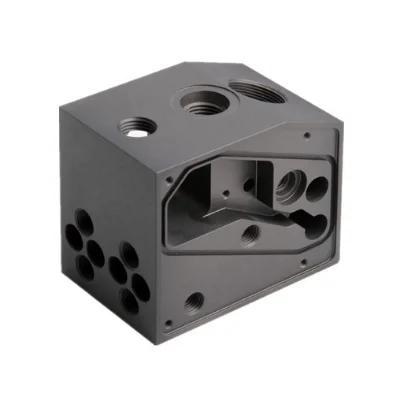
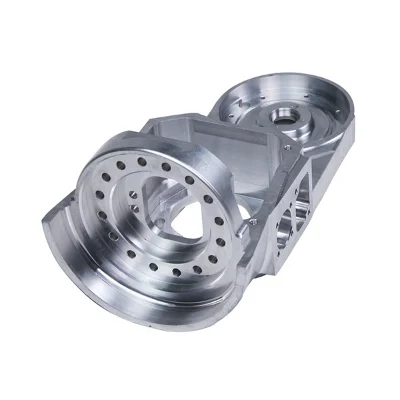
5-Axis CNC machining FAQs
Simultaneous 5-axis machining allows the cutting tool to move along all five axes at the same time, enabling more efficient machining of complex parts with intricate features. Applications include aerospace components, turbine blades, and medical implants.
Factors to consider include part geometry complexity, required tolerances, production volume, material type, and overall machining efficiency. 5-axis CNC machining is typically chosen for parts with intricate shapes or features that would be difficult to machine with lower-axis machines.
Operating a 5-axis CNC machine requires specialized skills in programming, tooling setup, and machine operation. Training in CAD/CAM software, machine kinematics, and toolpath optimization is essential for maximizing the capabilities of a 5-axis CNC machine.
Toolpath optimization involves calculating the most efficient toolpath for machining a part while minimizing tool changes and reducing cycle times. Optimal toolpaths enhance machining efficiency, improve surface finishes, and prolong tool life in 5-axis CNC machining operations.
Key considerations include tool geometry, material compatibility, tool holder stability, cutting speeds and feeds, and workpiece fixturing strategies. Selecting the right cutting tools and fixtures ensures optimal tool performance and part accuracy in 5-axis CNC machining.
Regular maintenance tasks for 5-axis CNC machines include spindle lubrication, tool holder and spindle taper cleaning, axis alignment checks, and machine calibration. Proper maintenance procedures help ensure the longevity and performance of 5-axis CNC machines.
While 5-axis CNC machining may have higher upfront costs due to machine complexity and training requirements, it offers improved efficiency, reduced scrap rates, and faster cycle times, resulting in overall cost savings in producing complex parts compared to traditional machining methods.
Yes, 5-axis CNC machining can be integrated with additive manufacturing processes for finishing operations or complex part features. It can also be coupled with robotic automation systems for loading/unloading parts and tool changes, enhancing overall manufacturing efficiency and flexibility.